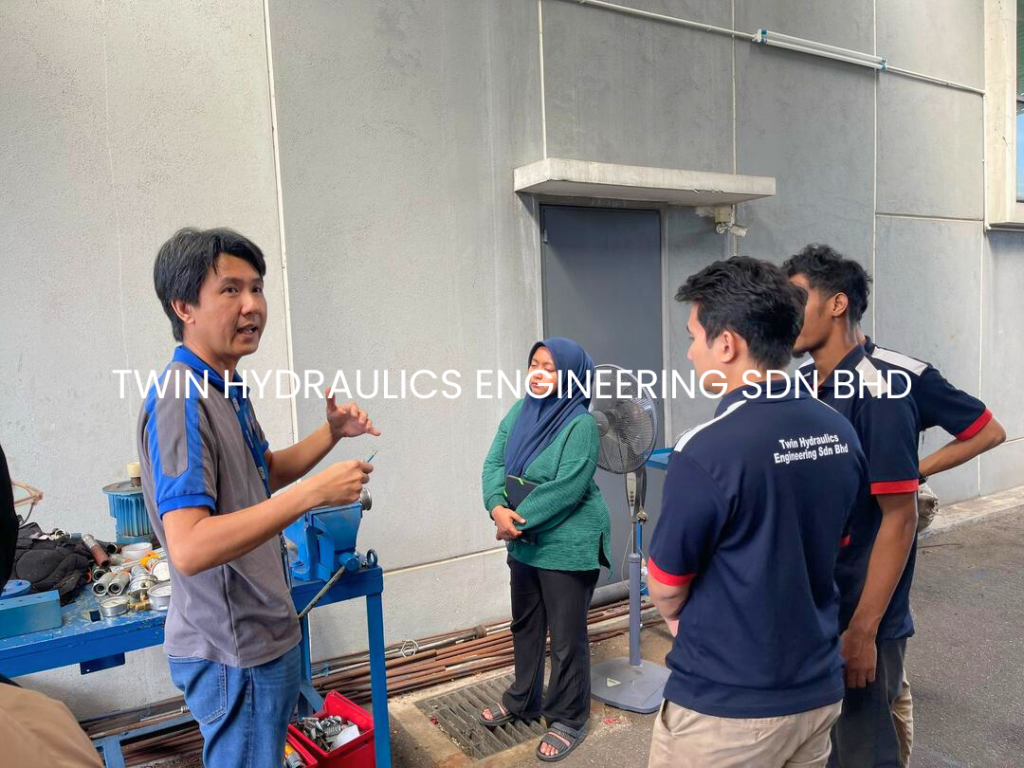
Our team has recently grown, an we’ve had the opportunity to learn more about pressure gauges. Not only technical engineering staff, but operational staff also have the chance to participate in learning about WIKA products. Our management arranged for WIKA to come to our office and conduct training for all staff. This training is valuable for expanding our knowledge, including how to remove the glass, clamp the pressure gauge, and correctly read its measurements.
A pressure gauge is an instrument used to measure and display the pressure of a medium. These devices feature elastic pressure elements and are widely used in various industrial applications. Depending on the application, pressure gauges may use Bourdon tubes, diaphragm elements, or capsule elements as pressure sensing components.
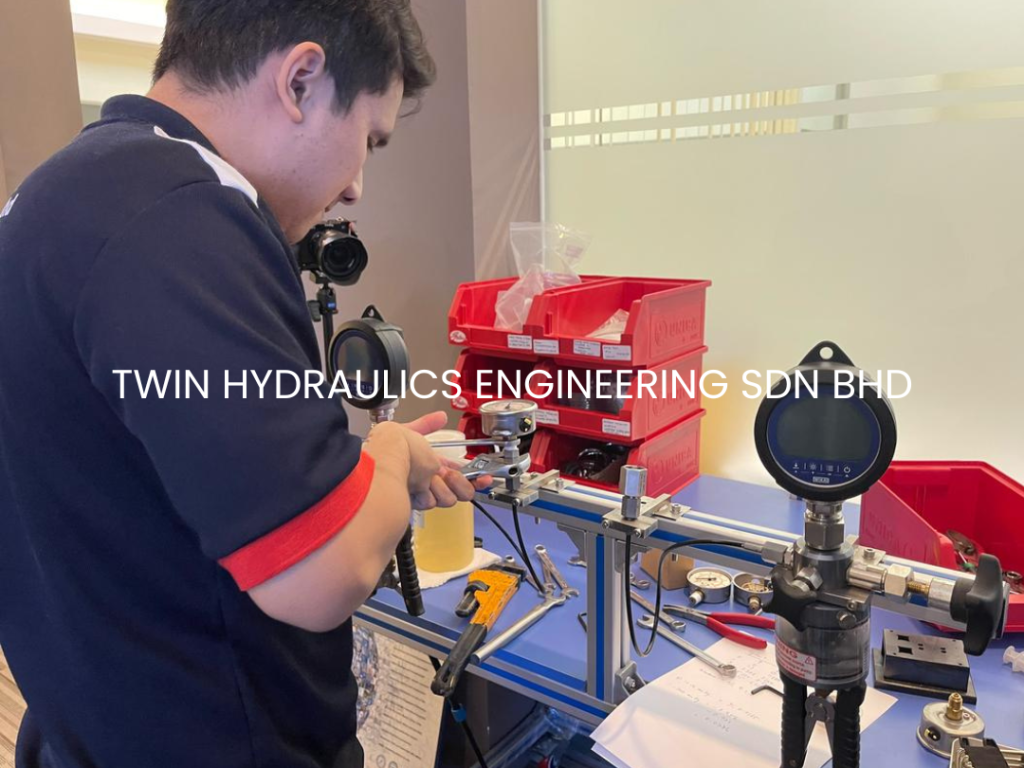
How does a pressure gauge work?
Pressure gauges operate differently depending on the type. Two main types of pressure gauges are used in industrial measurement: Bourdon tube pressure gauges and diaphragm pressure gauges. Each type has its own functional principles, making them suitable for specific applications.
- Bourdon tube pressure gauges measure pressure by using a Bourdon tube, which transmits the pressure directly to the pointer. The case contains a curved tube, which is filled with the medium. As pressure enters, the Bourdon tube stretches, and this movement is transferred to the gauge’s mechanism, moving the pointer and displaying the measurement on the dial.
- Diaphragm pressure gauges are used when Bourdon tube gauges reach their limits. In these gauges, the pressure is transmitted via a wave-shaped diaphragm to a link, which then transfers the pressure to the movement of the gauge.
The Bourdon tube Pressure Gauge, Model 213.53, with a copper alloy and stainless steel case, is available in liquid-filled versions. The wetted parts are made of copper alloy, and the case is constructed from stainless steel. This mechanical pressure gauge is manufactured by WIKA in accordance with the standards EN 837-1 and ASME b40.100
For safety, the instrument features a blow-out device that allows overpressure to escape in the event of failure. The case filling effectively dampens the pressure element and movement, making the gauge particularly well-suited for applications with high dynamic loads, such as rapid load cycles or vibrations.
The Model 213.53 is available in nominal sizes of 50 mm (2″), 63 mm (2 ½”), and 100 mm (4″), and it provides IP65 ingress protection. With an accuracy class of 1.0, this pressure gauge is ideal for a wide range of industrial applications.
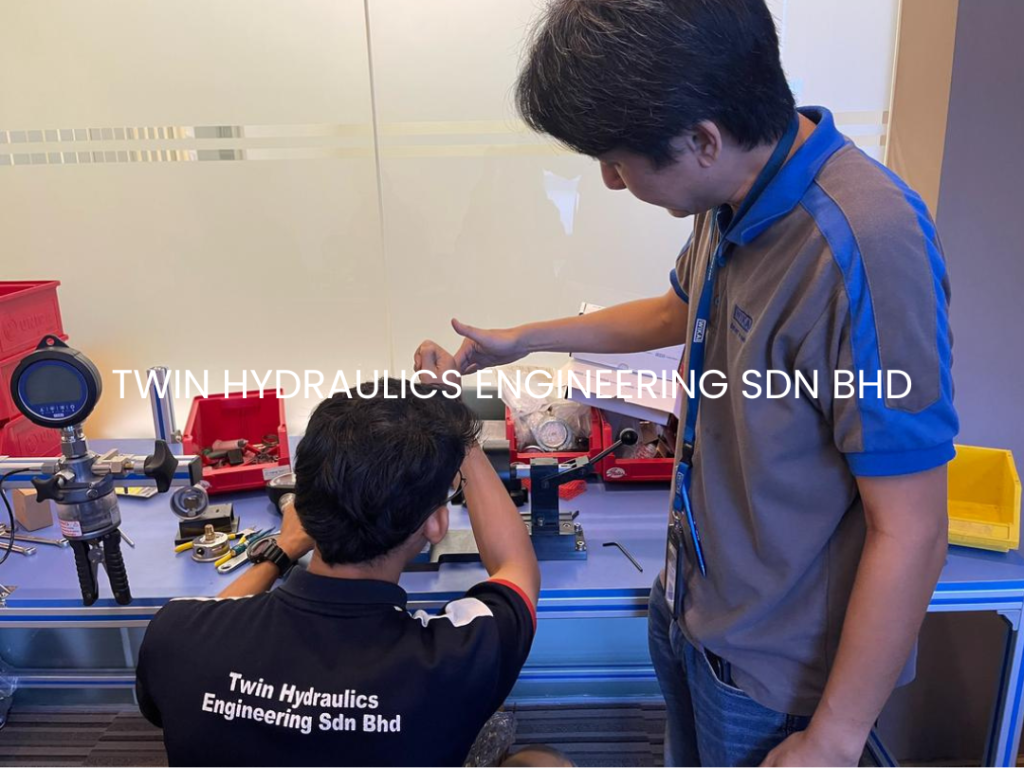
How to Calibrate a Pressure Gauge: A Step-by-Step Guide
Calibrating a pressure gauge is the process of determining the deviation between the gauge and a highly accurate reference instrument. Calibration ensures the accuracy of the pressure gauge by comparing its readings with those of a reference device known for its precise measurements. This process involves evaluating the full measuring range, including the zero point, intermediate values, and final readings, to detect any discrepancies. If the pressure gauge’s deviation falls within the manufacturer’s specified tolerance, it will be issued a calibration certificate. It’s important to note that calibration differs from adjustment-adjustment is necessary when the deviation exceeds acceptable limits, meaning the gauge does not meet the manufacturer’s standards.
This guide will help you understand the importance of pressure gauge calibration, the steps involved, and the distinction between calibration and adjustment to ensure accurate and reliable pressure readings.

We are glad to have participated in this training. We hope there will be more training opportunities in the future so that we can continue to expand our knowledge.